|
Focus |
Our goals |
|
Our performance in 2006 |
2007 and future targets |
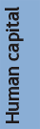 |
Safe work environments |
Work without fatal injuries and minimise work-related injuries |
|
44 fatalities (down from 46 in 2005). FIFR stable at 0.017 |
Integrate peer review findings and experience from others to reinforce the safety strategy.
The focus will be on risk management |
Reduce LTIFR by a further 35% to 0.5
Review contractor selection and integration into our safety programmes |
|
LTIFR for 2006 was 1.16 (23% higher than 2005). Anglo American’s core business going forward recorded an LTIFR of 1.58 |
An LTIFR target of 0.94 is set for 2007, representing a 40% improvement target for the new core businesses of Anglo American |
Healthy work environments |
Control workplace health hazards to avoid new cases of occupational disease and health impairment |
|
856 new cases (1,003 in 2005). The occupational illness incidence rate is up to 0.66 (from 0.65 in 2005) per 100 employees based on manhours worked |
Focus on reducing exposure to potential industrial hygiene hazards in order to minimise new cases of occupational illness |
Certification to third party health and safety systems will be at least 75% complete by the end of 2005 |
 |
86% of Group companies certified to
OHSAS 18001, AS 4801 or ISRS |
All material businesses will maintain certification |
Merit-based and empowering culture |
All managers/professionals have individual performance and development reviews (a large proportion of our workforce is subject to team-based targets and reviews) |
|
Performance reviews for more than 50% of all Anglo American employees, of whom 8.7% are managers |
Ongoing focus – key method of providing direction and development for our employees |
Progress towards employment equity targets in South Africa |
 |
43% achieved in 2006 – exceeds compliance target of 40% |
Continue transformation programmes and exceed the South African target |
Conduct Group communication survey |
 |
Ongoing improvement in employee
communication and sharing of knowledge |
Repeat Group communication survey in 2007 |
Evaluate and extend Group Information
Portal programme |
 |
Coverage of information portal (thesource) increased to 13,500 PC users. Growth in numbers of communities of practice and Group-wide access to information |
Coverage in all divisions. Continuous reinforcement of content and use of collaborative tools including specifically increasing the visibility of career opportunities across the Group |
HIV and AIDS |
50% VCT by the end of 2005 and 75% by 2007 in sub-Saharan Africa |
 |
VCT take-up of 63% exceeding the revised 2006 target |
70% VCT (long term 100%) in high disease burden countries |
Work in partnership with NGOs, governments and donor agencies |
 |
Launched community health centre in Bushbuckridge with multiple partners Various other community HIV/AIDS initiatives and programmes |
Sustain regional community HIV/AIDS initiatives, specifically those with external partners |
 |
Sustainable development integration into business model |
Sustainable development appraisal of investment proposals |
|
Ongoing |
All qualifying projects are
routinely reviewed |
Guidelines and practices |
Develop sustainable development toolbox
for engineers |
 |
Training undertaken in South Africa and Chile |
Training to be undertaken in Australia and toolbox to be published in 2007 |
Develop sustainable development guideline for planning capital projects |
 |
The initial guideline has been piloted on expansion and greenfield projects |
Refined guideline will be published
in 2007 |
Develop integrated mine closure guidelines |
 |
The mine closure toolbox has been
pilot-tested |
Further revisions undertaken. Publish in 2007, commence rollout and training |
Raise focus on product stewardship and recycling |
 |
REACH awareness raising complete Guidelines on material stewardship distributed |
Focus on implementation for REACH and roll out of materials stewardship approaches |
Engage key suppliers on sustainable development and business principles, practices and targets |
 |
Working drafts in circulation.
Divisional tools being developed. Further methodologies and tools being considered |
Supplier workshops and capacity building within procurement teams |
New target
|
|
|
Review policies and guidelines, specifically including environmental standards for air quality and water. Create integrated sustainable development framework |
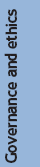 |
Transparency and reporting |
Increased stakeholder engagement on external reporting |
|
Extensive engagement through ICMM and GRI conducted. Research conducted on stakeholder perceptions |
Formal survey of public report stakeholders |
Corruption prevention |
Ensure quality and follow-up on speakup reports |
 |
181 calls received. Service suspended for legal reasons in France and Germany. Board involvement in implementation of EITI |
Raise profile of speakup and reactivate in France and Germany. Continued close involvement in EITI implementation |
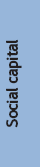 |
Corporate citizenship |
Finalise resettlement policy following international review of IFC safeguard policies |
 |
SEAT tool on resettlement produced |
Apply the tool where appropriate Progress the adoption of formal policy |
Implement training programme on security and human rights |
 |
Group level training provided in 2005, BU training taken forward in 2006 with increasing coverage of security contractors |
Support implementation where appropriate |
Develop human rights guidelines |
 |
Participated in the work of the UN Special Representative on Business and Human Rights and led ICMM’s work in the area |
Finalise human rights policy and guidelines |
Community issues |
Community engagement plans in place and improve the quality |
 |
Community engagement plans in place at over 95% of significant operations. Quality improved at those sites which have carried out initial SEAT assessments |
Continuous improvement of CEPs and encouragement of increased use of stakeholder forums to monitor progress and maintain dialogue |
45 SEAT assessments conducted |
 |
SEAT has now been conducted at 40 sites in 16 countries (a further 10 in pipeline).
Consultation undertaken on SEAT enhancements in 2006 |
Evaluate impact of SEAT implementation. Carry out SEAT assessments at 10 operations
|
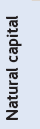 |
Systems |
Full ISO 14001 certification for material
businesses |
 |
86% certification – by turnover. No
certification has been lost. All new
operations are required to be certified
within two years of joining the group |
All material businesses to maintain
certification |
CO2 emissions and
energy efficiency |
A 15% improvement in energy efficiency
and a 10% reduction in CO2 emissions per
unit of production (emissions intensity) by
2014 |
 |
All businesses have targets in place
to achieve this goal. More than 1,000
projects underway |
Continue to drive the process
Improve accounting and
measurement |
Establish definitions, reporting boundaries
and determine the CO2 relating to transport
by 2006 |
 |
Initial results under review.
Ongoing refinement of data required |
Will finalise in 2007 |
Air quality |
Development of data on SO2 emissions from
fossil fuel use to be completed in 2005 |
 |
Completed – data on SO2 emissions
from fossil fuels obtained by using
internationally reputable sources |
Included in numbers |
Water efficiency |
Efficiency targets in water-stressed areas |
 |
All business units have set targets
appropriate to their businesses and sites |
These will remain site-specific
objectives |
Biodiversity |
Biodiversity action plans (BAPs) to be integrated into ISO 14001 systems at significant sites
Peer review of 10 BAPs
|
 |
A further 14 sites were reviewed through the peer review programme. Integration into ISO 14001 systems achieved at most operations |
Ten sites to be reviewed in 2007 Continue to integrate biodiversity into management systems |
Continue working with ICMM and leading conservation organisations |
 |
ICMM involvement ongoing. Engagement with, among others: Fauna and Flora International, Business and Biodiversity Offset Programme, Conservation International, Earthwatch |
Continue with partnerships at
all levels |
Assess the Group’s exposure to
protected areas |
 |
The Group has a low-risk, well-managed exposure to protected areas. Based on the 2005 assessment, it was decided to reduce the frequency of the assessment |
Review in 2008
|
Responsible land use |
Closure plans for all managed operations will be updated regularly and fully costed |
 |
Due to exclusion of non-core businesses, provision for closure liability has been reduced to $747.5 million at the end of 2006 from $1,088 million in 2005. No reduction in remaining core businesses |
Ongoing |
Waste management |
Group tailings risk assessment for high volume waste management |
 |
Risk report produced annually |
Continue managing high-impact,
low-likelihood risk |
Expand tailings guideline document to include waste rock, heap leach pads, backfilling and slag disposal |
 |
Work on heap leach pads, waste rock and backfill is to continue. No start has been made on slag disposal |
Project to be completed and guideline to be applied |
Establish baselines for all waste volumes in 2006 and reduction targets in 2007 |
|
Most baselines established, focus on targets and reduction |
Baselines have been set and targets will be managed |