As pressure grows to reduce the amount of waste being landfilled, Anglo’s Technical Division is working with a number of business units and entrepreneurs to find commercial solutions for waste products such as slag, gypsum, rubber and weathered coal. A number of product prototypes have been developed and are being subjected to tests for strength and durability. If successful, they could soon be launched on the South African market for use in the construction industry.
Our most significant waste stream is mining waste which is stored on site and inspected regularly for compliance with Anglo American’s waste management guidelines. Waste facilities on our properties conform to local requirements.
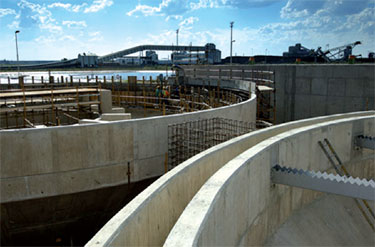
Construction of the Emalahleni water treatment plant nearing completion.
|
2005 |
2006 |
Core businesses |
Total number of process waste
disposal facilities |
174 |
168 |
121 |
Number of facilities in active use |
96 |
91 |
68 |
Total area occupied by facilities (hectares) |
9,454 |
7,340 |
5,698 |
Total number of audits (third party and in-house) |
124 |
121 |
80 |
In the UK, more than 50 million tyres are removed from vehicles each year. While some can be re-used, retreaded or recycled, the disposal of the balance remains a problem.
New legislation forbids disposal of tyres in landfill sites. Buxton Lime Industries, part of the Anglo Industrial Minerals business unit, has been conducting a trial to use tyres as an alternative to fossil fuels in its Tunstead cement plant.
Tyres could replace up to 25% of fossil fuels used by the cement plant at Tunstead, helping society to deal with a waste problem and simultaneously reducing Tunstead’s CO2 emissions.
After extensive consultation, the UK’s Environment Agency gave permission for a trial in September 2006. The Agency requires strict adherence with its Substitute Fuels Protocol.
A £2.3 million ($4 million) tyre storage, handling and delivery system was installed at the plant and, after a commissioning and set-up period, the use of tyres as an alternative fuel began in November 2006.
The tyres are sorted and chipped by a company in Yorkshire before being transported to Tunstead by lorry. Chipping the tyres optimises their use. As one tonne of tyre chips replaces one tonne of coal, the total lorry movements to the site remains the same.
The tyre chips are completely combusted in the 1,450ºC process, so there is no smoke or odour and no waste is produced.
Dr Martyn Kenny, technical and environmental director for Buxton Lime Industries, says the company is optimistic about the success of the trial and sees it as the first step in its alternative fuels programme.
Mantos Blancos, near Antofagasta in Chile, has found a socially beneficial business solution to reducing the environmental liabilities created by the giant tyres used by haulage trucks. The operation is selling the tyres to recycling companies which strip the steel wire from the tyre core and reduce the rubber to pellets. This frees up space currently used as a waste dump and will reduce the cost of transferring and handling the tyres, with potential energy savings. The resources earned will be donated to the local community to improve their facilities and projects. About 350 of the giant tyres have been sold.
Lead anode wastes and slimes containing lead from the electrowinning process at Mantos Blancos mine near Antofagasta, Chile are now being recycled.
About 30,000 kilograms (kg) per annum of solid waste lead is generated from the electrowinning anodes once they are scrapped at the end of their useful lives. Recycling of this material is expected to achieve a significant 20% reduction in the annual cost of anodes.
A further 25,000 kg of lead is contained in the residual slimes that collect, over time, at the bottom of the electrowinning cells. These slimes have been stockpiled in a purpose-built containment area for the past decade. Reprocessing began in 2006 to extract the lead in this residue material for which Mantos Blancos receives a rebate from the anode manufacturing company when new anodes are purchased.
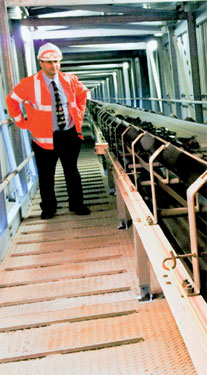
Hasan Bobat, fuels development engineer at Tunstead, standing next to the conveyor belt.
|