 |
 |
 |
 |
 |
|
 |
|
|
 |
|
|
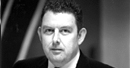 |
It is our remarkable level of service
that
differentiates us from our competition >>>
Richard Butler,
Chief Process Officer |
|
 |
 |
 |
 |
|
The Group Processes provide the global platforms that
enable all our businesses to provide our customers with
outstanding service. This structure allows the Group to
benefit from shared best practice and cost effectiveness
through economies of scale. It is the investment that
we have made in these platforms and, critically, the knowledge
of how to make them really work that creates many of the
significant barriers to entry.
The total cost of the Processes in the year was £69.3m,
up 5.5% from £65.7m last year. Most of the increase
is due to increased investment in Information Systems
and internet development.
Supply Chain
Supply Chain has delivered improved customer service and
greater stock holding efficiency. The ability to satisfy
every customer order, in full and immediately, is the
key measure of Supply Chain performance – we call
it “orderfill”. Throughout the year there has been a consistent
improvement in performance. It is this remarkable level
of service, significantly over 90% in our major RS markets,
that differentiates us from our competition. This level
of orderfill requires approaching 98% availability for
each product ordered. Nine of our businesses achieved
monthly orderfill records in the year, and the overwhelming
majority of RS customers are now served by businesses
with over 90% orderfill levels.
Supply Chain is responsible for delivering orderfill whilst
managing the Group’s total stock. As a consequence of
further investment in stock management systems, and leveraging
expertise across the whole Group, stocks have been managed
tightly. This has resulted in an increase in stock turn
from 2.5 times to 2.7 times and an 18.0% reduction in
stock from £164.8m (in continuing operations) at
the start of the year to £135.1m.
Facilities
This central team takes responsibility
for maximising the efficiency of our Distribution Centres
and project managing new developments. In Italy, the
move into larger leasehold premises was
successfully completed in December 2001, and the move
to new offices took place in April 2002. In Germany, development
of an 82,000 square metre greenfield site at Bad Hersfeld
is well advanced and the facility will be ready for occupation
in December 2002. In the year, capital expenditure on
these projects was approximately £17m.
Product Management
Our total product offer is approximately 300,000 products.
Product Management works closely with customers and suppliers
to ensure that key new products are introduced to appropriate
markets and that the range is refreshed as existing products
are further developed.
Because of our unique global presence, large number of
customers and detailed customer knowledge, our suppliers
are very keen to work closely with us. They recognise
our wide customer reach in, for example, the important
research and development arena, and value highly the opportunity
to enhance their market understanding by selling through
us.
Another good example of this is the strategic alliance
with Avnet, now entering its third year. Both revenue
and logistics benefits have been delivered, and pilots
are currently underway testing how we can work more closely
together, by leveraging RS’s ability to service some elements
of the small order requirements of Avnet’s customer base.
Media Publishing
Last year’s catalogue production led to the printing of
over 5.5 billion pages, with all the paper sourced from
renewable forests. Each catalogue, and supporting CD and
website, is published by the Media Publishing Process
in local language, including Japanese and Chinese versions.
Further rationalisation of paper and print contracts has
delivered lower unit costs for media production. Investment
in the latest desktop publishing technology has also enabled
the internal production of more marketing material, such
as the “RS@Work” specialogue, reducing both costs and
production time.
This year has seen the establishment of a Content Management
organisation specifically focused upon the creation, maintenance
and control of all product-related data including technical
support data. Demand for technical data is as strong as
ever, and during the last year our technical data on the
internet was accessed 1.3 million times worldwide.
Human Resources
Across the Group the recruitment, development and retention
of our management teams is a top priority. The Group team
facilitates the detailed management resource planning
that takes place. This gives us a view of the management
needs of the future, thereby enabling effective and focused
development and recruitment activity.
Subject to shareholder approval at the Annual General
Meeting in July, the new Long Term Incentive Share Option
Plan will then be launched. Plans are well advanced for
an effective communication programme to ensure the Plan
is well understood and to maximise its impact, as both
an incentive for the key management population and to
aid their retention.
Information Systems
Though responsibility for our Information Systems process
falls within Jeff Hewitt’s area, for the completeness
of this Process Review, I will comment on this important
area.
Information Systems accounted for some 40% of total Process
costs, or £28.3m, an 18.9% increase on last year.
Included in this cost are all the labour and depreciation
expenses of the development activities and support infrastructure
for the Group’s operations, including e-Commerce.
During the year capital expenditure in information systems
increased substantially to £26.7m with the development
of the major enterprise systems programmes in Europe and
Asia that we have previously indicated. These will amount
in total to c.£50m over three years (and over £40m
in Europe). Within the programmes: the infrastructure
investment to enable more effective and secure
communications and data sharing across Europe and Asia
has already been completed; common approaches to our customer,
product and supplier databases are increasingly in place;
robust networks for our e-Commerce expansion have been
established; and work on implementing more standardised
operating procedures and system environments is in progress.
Initial implementation of these new procedures is planned
for this year in France and Singapore, and full roll-out
across Europe and Asia should be completed by the middle
of 2004. Within the Asia programme the upgrading of systems
in China represents an important further investment in
that market.
The impact on our costs of the enterprise system projects
was £1.8m in the year. This impact will increase
significantly in future years through higher depreciation
resulting from the capital expenditure. Meanwhile the
costs of our existing systems are being reduced. Though
the changes required in our businesses by this investment
programme will incur cost, we believe that substantial
efficiency benefits and rewards from enhanced customer
service will be achieved. The internal and customer facing
platforms now being established are critical enablers
to meeting our strategic goals.
The Euro conversion programmes were also completed during
the year to enable full Euro trading and to convert the
accounting bases of relevant companies to Euros. These
transitions required considerable management effort and
cost about £0.8m.
Summary
In summary, this has been a year
of real progress for the Group Processes. Even in difficult
trading conditions the level of service to our customers
has been maintained and in many areas enhanced. At the
same time, each Process has contributed to the overall
effectiveness of the Group’s performance and development.
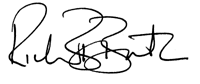
|
|
|
 |